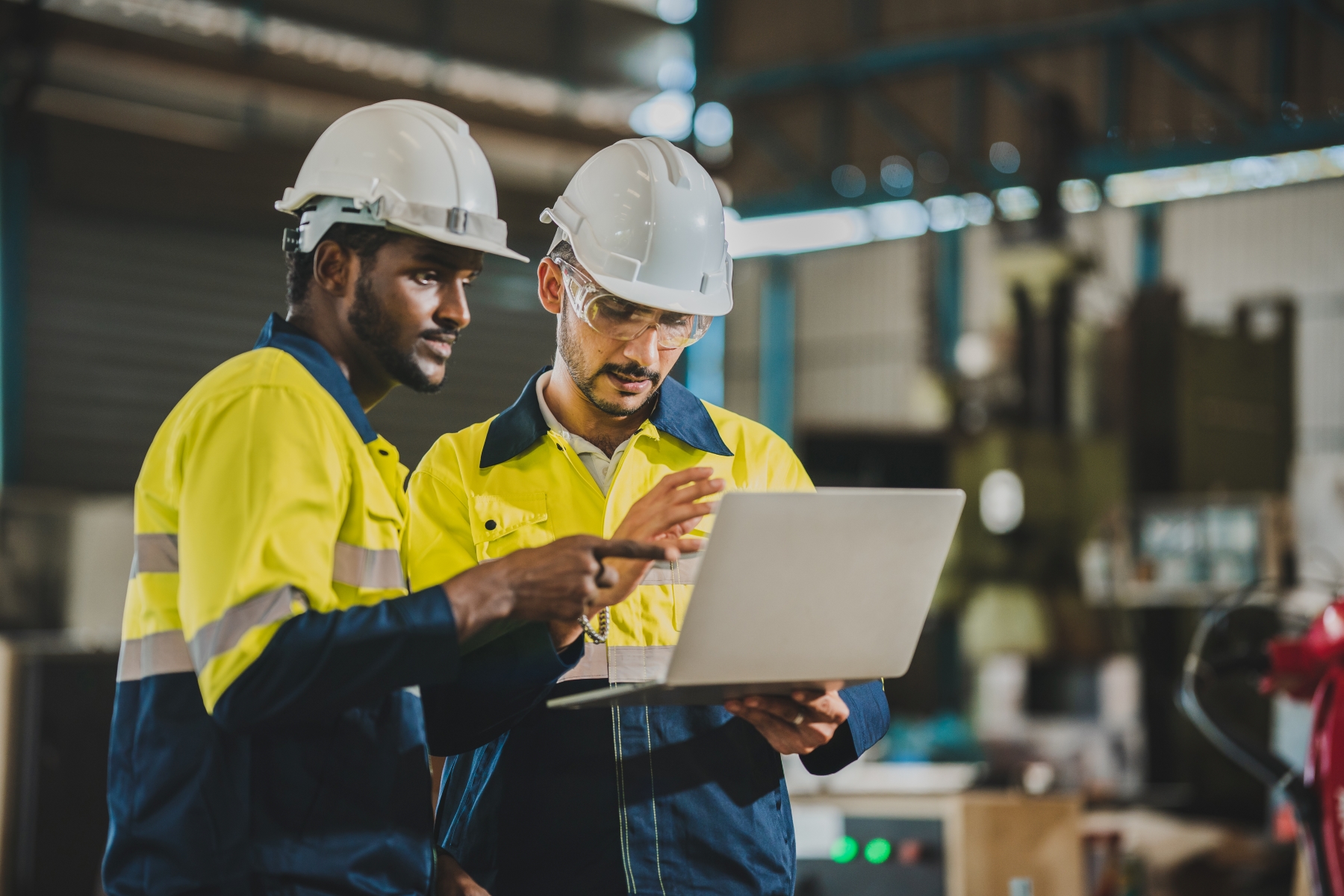
Top Considerations When Implementing a New Cost Accounting System for Your Manufacturing Business
Today’s manufacturing environment is more complex than ever, and bills of materials have increasingly longer chains that require accurate costing. An effective cost accounting system should provide robust cost accounting by tightly monitoring and tracking all cost elements of purchased and manufactured products. Implementing a new cost accounting system can be an enormous project that starts with identifying a system that best fits the needs of your manufacturing business.
As your company is contemplating a change in its accounting software, it should consider the following.
Manufacturing Cost Accounting System Users
Cost accounting systems often fall short because they fail to produce meaningful information for users across the organization. The system is usually geared towards the needs of those who manage it and may not provide useful information to other departments. It is critical that the project team includes users across the organization and establishes clear objectives during planning to ensure the redesigned or new system will meet the needs of its users.
Assessment of Current Manufacturing Cost Accounting System
A business must thoroughly review its requirements and the technology used to support it. A business needs a clear vision for its short- and long-term needs and anticipated changes and objectives. You must also have a robust understanding of your current system, as most businesses do not use the system to their full potential. After a complete evaluation, you can decide whether to continue with your current system, tapping into its unused functionality, or proceed with a new one. A new system must be the right fit, not only for today but also for the future.
Stand-Alone Manufacturing Cost Accounting System vs. ERP
A stand-alone accounting software with a cost accounting module is more cost-effective for small businesses but may have limited capabilities. Integrating a stand-alone accounting system is simple and requires minimal support. An enterprise resource planning (ERP) software system may be a better fit for medium and large-sized businesses as it provides robust capabilities and integrated functionality across the organization. The integration of an ERP can be complex and require more support.
Manufacturing Cost Accounting Method
You must consider your costing method (i.e., standard, LIFO, FIFO, average cost, etc.), overhead allocation methodology, and other practices when contemplating a new or redesigned system. Below are a few things to consider:
- Do you use multiple costing methods?
- Do you specify the cost method by product or SKU?
- Do you track numerous costs per item?
- Do you use multiple methodologies for the allocation of overhead?
- Do you track the cost of inventory transferred between subsidiaries, divisions or locations?
The decision to implement a new cost accounting system can be daunting. A manufacturer must establish clear objectives across the organization, assess its current system and consider its specific needs, including the complexity of its costing and overhead allocation methods. Please contact us to help navigate this challenging process.