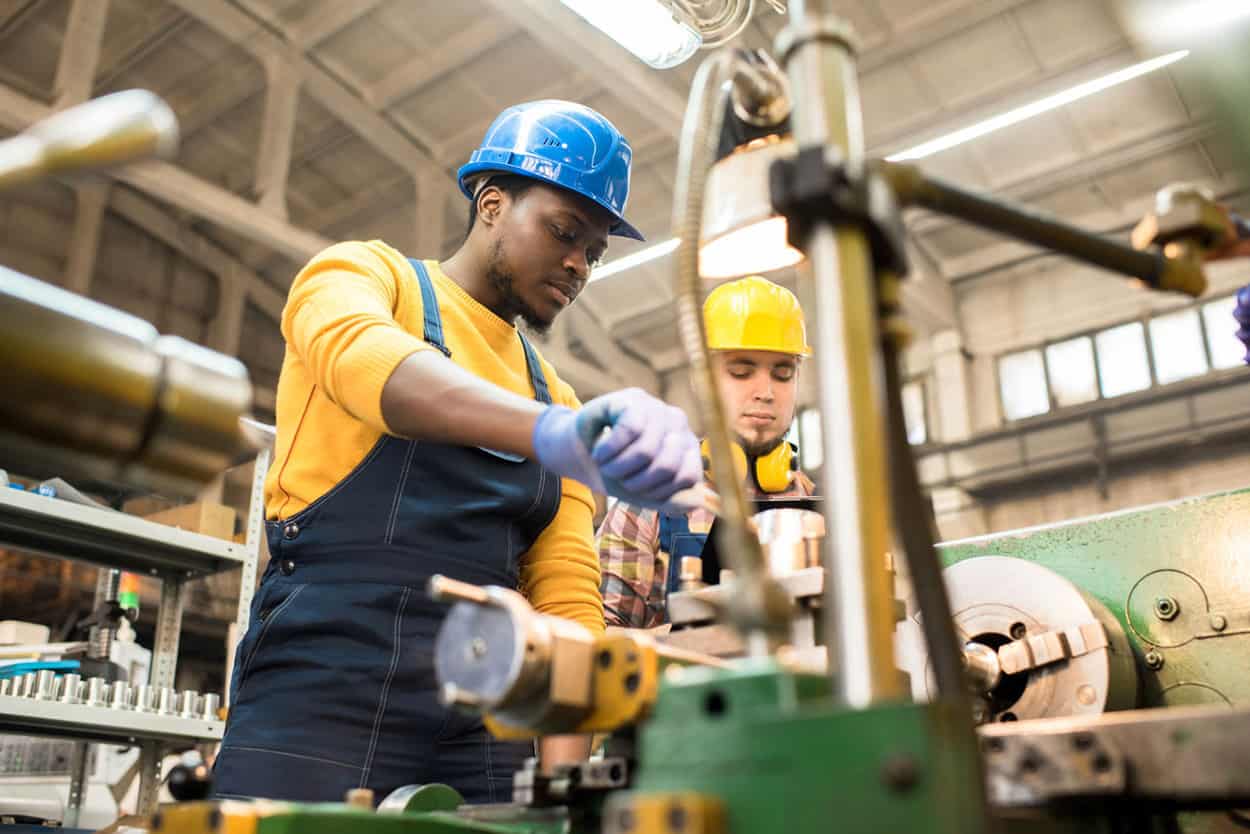
Manufacturing Industry Outlook: Exploring Rising Labor Costs, Employee Shortages and Supply Chain Disruptions
Across the manufacturing and distribution companies we serve, we continue to hear that labor costs, employee shortages and supply chain disruptions are rising, even as more people are receiving the COVID-19 vaccine and the effects of the pandemic continue to lessen. In general, manufacturers saw significant declines in demand and production at the onset of the pandemic during the first half of 2020. There has been an uneven recovery from this decline throughout the second half of 2020 and into 2021, which varies from sector to sector. For many manufacturers, product demand has been rapidly increasing, which is likely to continue.
Many factors are contributing to manufacturing labor shortages and rising labor costs, including school shutdowns for in-person classes, challenges to finding affordable childcare, expanded and extended government unemployment benefits and employees finding opportunities in remote positions or other industries altogether. Whatever weight each factor is driving, recruitment and labor retention at all skill levels remains a challenge for employers. While the pressures on the labor market are expected to ease as more people are vaccinated and the broader economy improves, labor costs are expected to be higher than before the pandemic.
Companies should prepare to continue operating in uncertain labor and commodities markets. The quality of a company’s inventory costing system and budgeting and forecasting models will drive how successful each company is at protecting gross margins through these uncertainties.
Inventory costs should include the cost of raw materials plus the cost to convert those materials into a finished product, including labor and overhead costs. Your accounting system should be capturing the labor costs for employees who work directly on manufacturing a product as well as the indirect costs of employees whose work is required to manufacture the products, such as plant managers and employees who maintain and repair manufacturing equipment. Labor costs should include both wages and related employee benefits such as health insurance and retirement plan costs paid by the company.
Many companies use a standard costing system for inventory which often is only updated annually. These standard costs should be reviewed and updated on a more frequent basis as materials, labor and supply chain costs have increased throughout the pandemic.
In addition to ensuring your accounting system is appropriately reflecting the true cost of inventory, forecasting and budgeting models should be reviewed to ensure that changes in labor costs are built into those models. For products in high demand, many companies have been able to negotiate price increases with customers, including big box retailers that have traditionally been resistant to allow changes to established pricing schedules.
Finally, companies should review their compensation and benefits packages to ensure that they are remaining competitive. Manufacturers should also invest in training and equipment that can increase the productivity of each employee.
While some relief to the tight labor market may be on the horizon, companies who understand the true cost of their inventory will be better positioned to navigate what will likely continue to be a fluid labor and commodities market. If you need assistance with developing or updating your inventory costing system, the Moore Colson team is available to help. Contact us for more information.